
So, food for thought, if you're in the planning phase and deciding what to do. My current build will have a 60,000 RPM spindle, which I've measured as having 1 micron of runout (shown in attached photo) and should therefore be great for milling PCBs, but the same spindle isn't well optimized for, say, milling aluminum or steel, which would be better done by a slower, higher power spindle. I was aiming to have a single "do everything" CNC, but retrospect, I think an argument can be made for having a small CNC for PCB work and a separate larger machine for handling other things. I'm presently assembling a 6040 machine, and I expect it will go well, but the fact is that deflections on a 3020 machine, given comparable construction, are far less, as simple physics tells us. For milling PCBs, small machines are actually better. As long as it's not bottoming out inside the spindle, you're good. Although the standard instruction is to insert the bit so that it protrudes just barely beyond the back of the collet by around 1/8" or so, the fact is that an extremely easy way to greatly reduce runout is to insert it much farther inside than that.
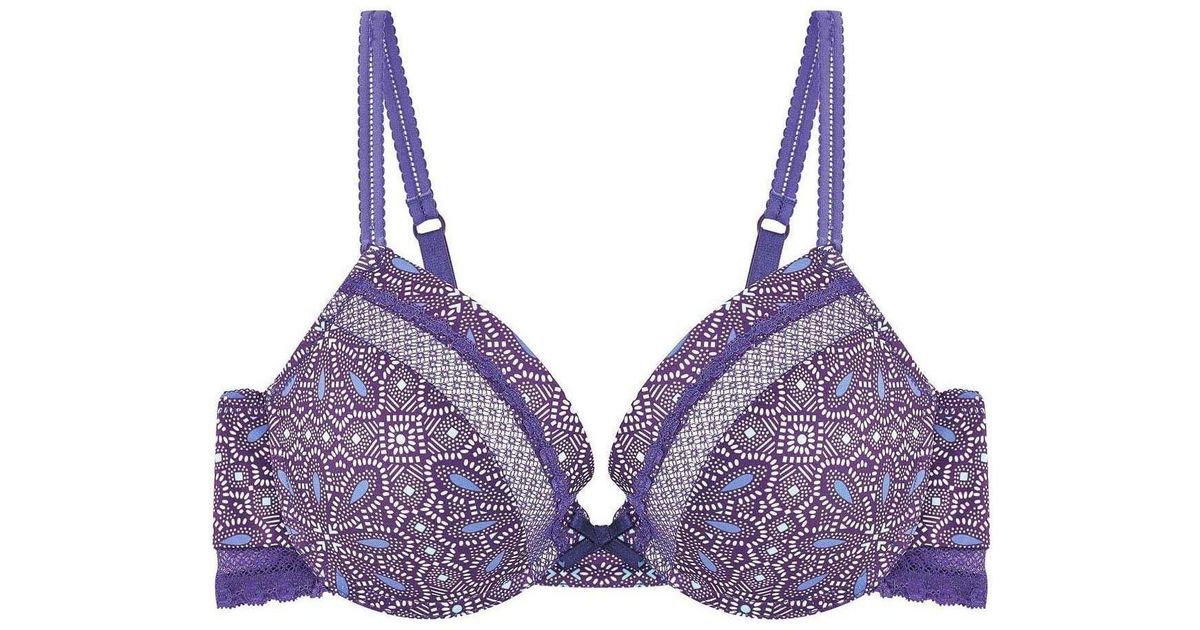
Now, in retrospect, this may seem obvious (especially to those in the know), but I notice that even Ave got this wrong, so I don't feel too bad for having made this ignorant mistake. the proper way to insert the collet is to first snap it into the nut and only afterward insert the bit.


Reporting back on a few things that I either didn't realize or perhaps didn't fully appreciate when I first undertook the earlier CNC above, and which may benefit others.
